Ready Mixed Plants
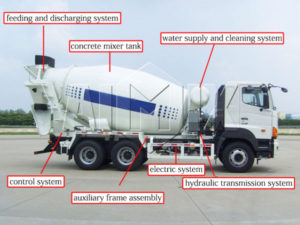
Ready Mixed Plants
Ready-mixed concrete (RMC as it’s commonly called), refers to concrete that is specifically batched for customers (mainly main contractors) and supplied to them as a single product. The concrete is batched out through Ready Mixed Plants.
Batch plants are by far more precise in composition mixing based on the design mix specified by the design consultant / engineer. It also allows traceability in the unlikely event of issues that surface due to concrete failure or incompatibility. The lifespan of a good concrete ready mixed plant will normally outweigh the cost if properly maintained.
Advantages of RMC
- Precision amount of raw materials is combined and mixed at each and every batch.
- Ability to add on admixtures that are required for the targeted type of concrete to improve the performance of concrete by adding admixtures. Examples of admixtures being used are to:
- reduce water requirements
- entrain air into a mixture
- add fibres to improve strength
- Self-Compacting Concrete (SCC)
- Since the raw materials are accurately weighed and mixed before discharged, the quality of concrete is assured. There is a strict basis of traceability in the process parameters and possible continuous monitoring to allow consultants to check on the design mix versus the batch concrete and that is proven internationally viable.
However, the above will not hold true if there is poor control on the raw materials, batching and mixing methods in the ready mixed plant. Hence independent consultants can provide this assurance if needed.
The use of admixtures requires precision in dosing and mix design which is more difficult, though not impossible, without the automatic dosing/measuring weigher in the ready mixed plant. This is especially true when the volume of the targeted design concrete is high and manual labour will cause issues when fatigue / human error kicks in. It is also paramount that the design mix of the products are thoroughly tested in the laboratory prior to mass production in the plant. This allows adjustments if needed without causing too much financial loss.
- The speed which the ready mixed plant can produce high quality concrete continuously provides a lot of comfort in fast track project construction plans. This allow continuous casting on site without sacrificing undue loss of construction time and possible cold joints.
Disadvantages
- Concrete shrinks as it is placed and cured. Hence cracking and shrinkage issues will occur if the design engineers and contractors do not take it into account during the planning and design stage. An example is to place expansion joints to prevent the cracking from occurring when casting large slabs.
- Most of the RMC are transported to the site via 6-9m3 mixer trucks. These mixer trucks agitate the concrete continuously during transportation. However, the sheer size of these trucks is an issue and hence careful planning of the ROA (route of advancement) is critically needed.
- There is also a need to have checkpoints on site (usually along the site access roads for the trucks) where samples of the concrete are taken. This is a part of the quality control system prior to placement and allows for further traceability should unforeseen issues occur.
- Generally, concrete must be placed within 45mins. The time can be extended if there is a foreseeable delay expected but this delay has to be pre-planned and worked into the design. If the delay is during placing or caused by a supply interruption, then cold joints will occur and financial loss is expected. This loss can balloon to a large amount in the case of mass concreting.
The post Ready Mixed Plants appeared first on Construction & Property News.
Source: construction property news